How Can I Get My Wooden Parts Delivered as Fast as Possible?
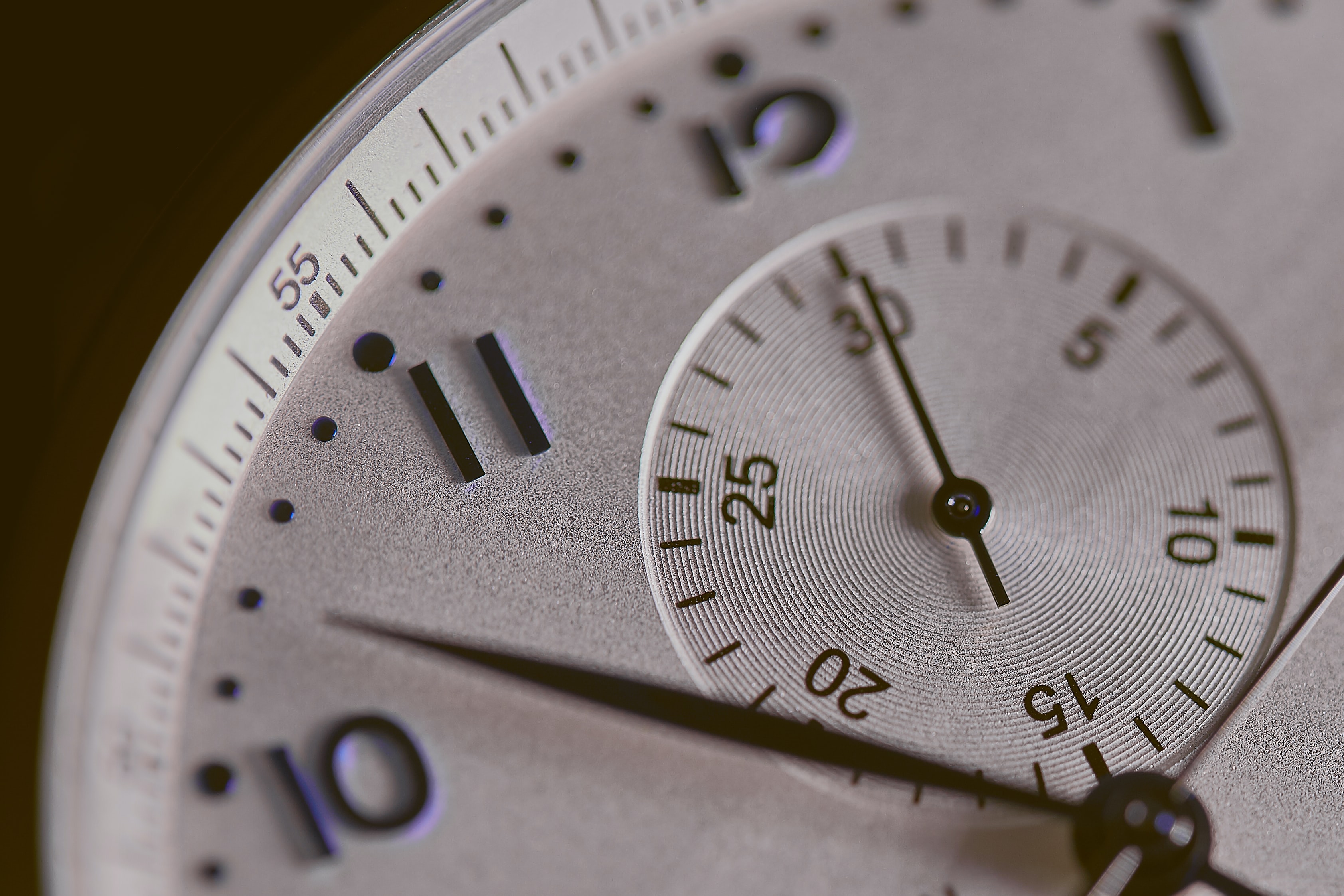
How to order on time
The average lead time between submitting your order and having it delivered to your address can vary greatly depending on a variety of factors which we will mention in this article. However, the safest bet to ensure that your project will be delivered on time, is to start preparing your drawings and files well in advance. We recommend adding an extra 2 weeks to be on the safe side.
Make sure your drawings are ready for production immediately
The first big step that determines the lead time of your order is the complexity of your project and the quality of your drawings. Read the 11 ways you can make sure your drawings and files are ready for production in one go. Apart from saving you time, preparing your drawings will save you costs as we won’t need to include this cost in your quote. The 11 tips are listed below and are described in more detail in this article.
1. Avoid extremely thin walls or components in your design
2. Avoid parts that cannot be CNC-milled at all.
3. Design cavities based on rules of thumb about depth/width ratios
4. Take into account curves of inside corners
5. Add "dogbones" to allow parts to fit together
6. Avoid designing cutouts that are too small
7. Design holes with standard dimensions
8. Adhere to standards for doors and shelves.
9. Adhere to standard dimensions for dowel holes.
10. Draw your hinges correctly.
11. Consider adding baseboards when drawing cabinets
Choose standard materials
The delivery time of the raw board material forms a significant part of the total lead time it takes to get your order completely ready. To ensure that you spend as little time as possible on this, choose as many common or widely used materials as possible with their standard thicknesses. Common wood boards are: MDF, Chipboard, Underlayment, OSB and Plywood. Normally these boards are in stock at suppliers in the Netherlands. The delivery time in that case is a few days. To ensure that no time-consuming additional processing needs to be carried out on the raw board material to get it to the right thickness, we recommend that you base your design on standard thicknesses of board material. These standard thicknesses are: 12, 15, 18, 22, 25, 30, 32 or 36 millimeters. Each material may have different standard thicknesses, so we recommend you research these first.
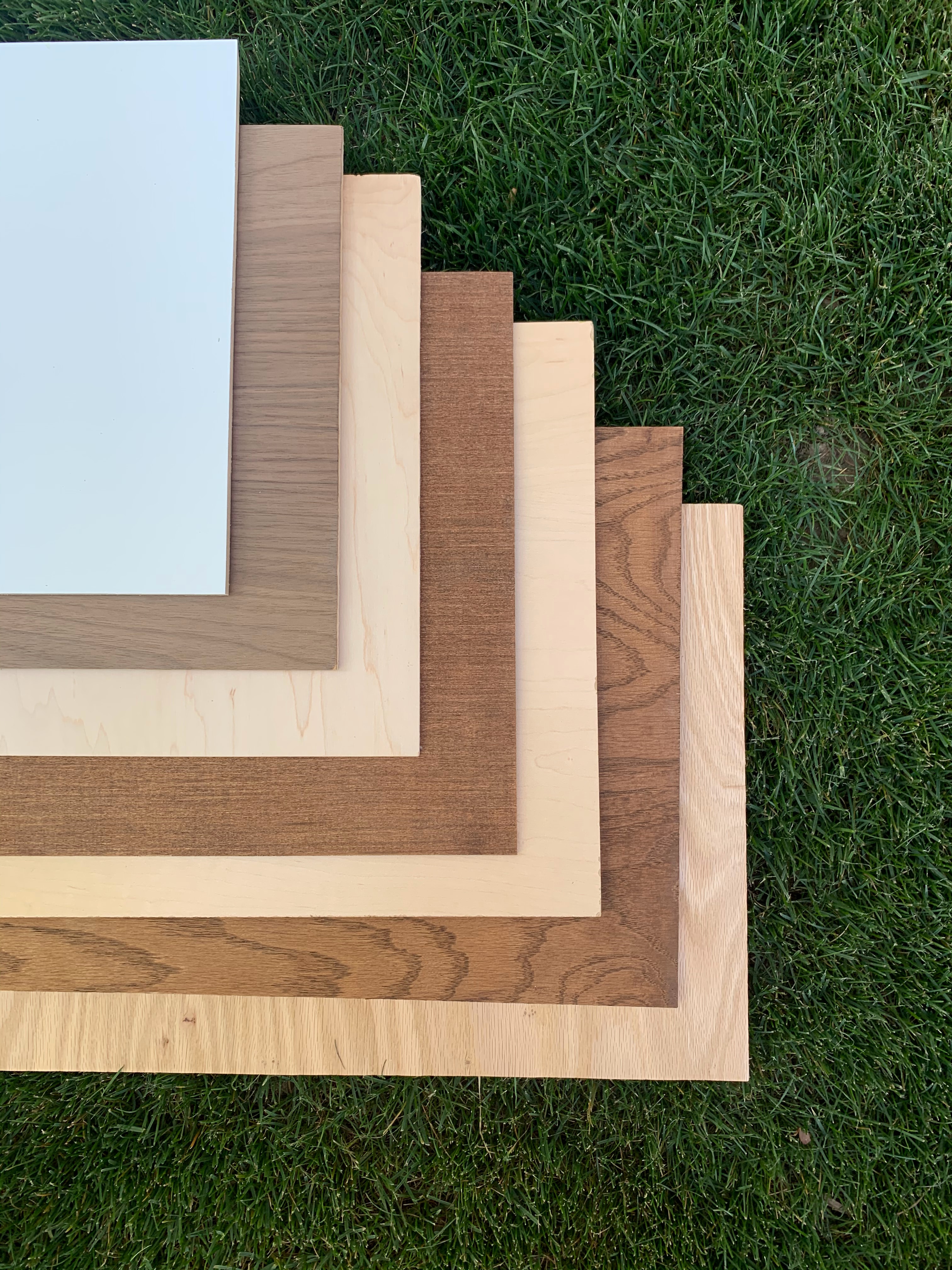
Avoid extra time for finishing
Sanding, oiling, spraying, painting and edge banding of milled parts also takes extra time. While these operations ensure that your project will look well finished, they are also often time-consuming and carry extra costs. You can save lead time by designing your project so that these operations are not necessary or are not performed until a later stage.
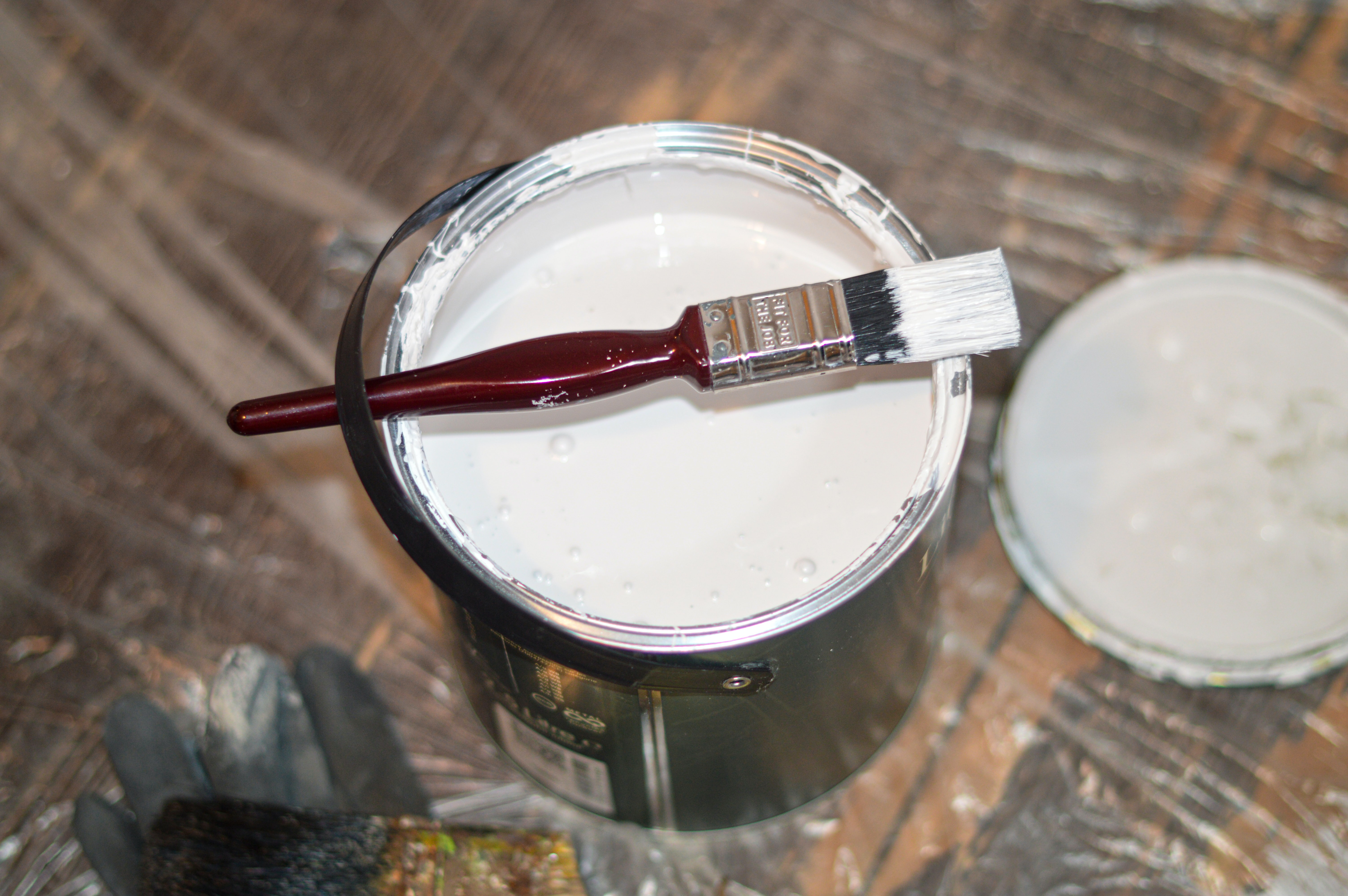
Provide as much relevant information as possible
The above tips for reducing lead time are easy to overlook and relate to (design) choices you can make in advance. But in some cases unnecessary time is lost during the production process or during assembly of the various parts. This is because digital drawings or sketches do not always automatically take into account the physical limitations of the machine. Also, design errors in the drawing are not always visible. To prevent this as much as possible, it is important that you include all relevant information when uploading your project. How do the different parts ultimately fit together? Where will the project stand or hang? What are the different parts for and what do you want to use them for? By sending this information along, the manufacturer already has a picture of the end result during production and you avoid unintentional mistakes and therefore extra (repair) time.
Pay a rush fee for a shorter turnaround time
In some cases it will not be possible for you to take the usual lead times into account. If you have a tight timeframe in mind, you may want to consider a rush order. Because the lead time depends on factors such as complexity and delivery time of materials, it is important that you contact us first to ask about the possibilities. Each order is evaluated on a case by case basis. We’ll give your project priority and do our best to find a solution. In this case, we will charge a 20% rush fee of the quoted value. In consultation we can determine whether it is feasible to produce and deliver your order in a shorter time frame, and we’ll explore other possibilities to further reduce the lead time.
Conclusion
To sum up, if you need your wooden parts to be delivered on time it is important to start as soon as possible. You can save time by optimizing your project for production upfront, choosing standard materials that are in stock and only do the most necessary finishes. On top of that you can consider paying a rush fee for an even faster turnaround. If you have any questions about delivery times, don't hesitate to contact the Cutr team via email or chat.
Related articles:
How-wooden-interior-projects-can-be-manufactured-and-finalised-3x-faster
How to make your design ready for production
Upload your design file and get a quote
within days
Quality production with trusted production network.
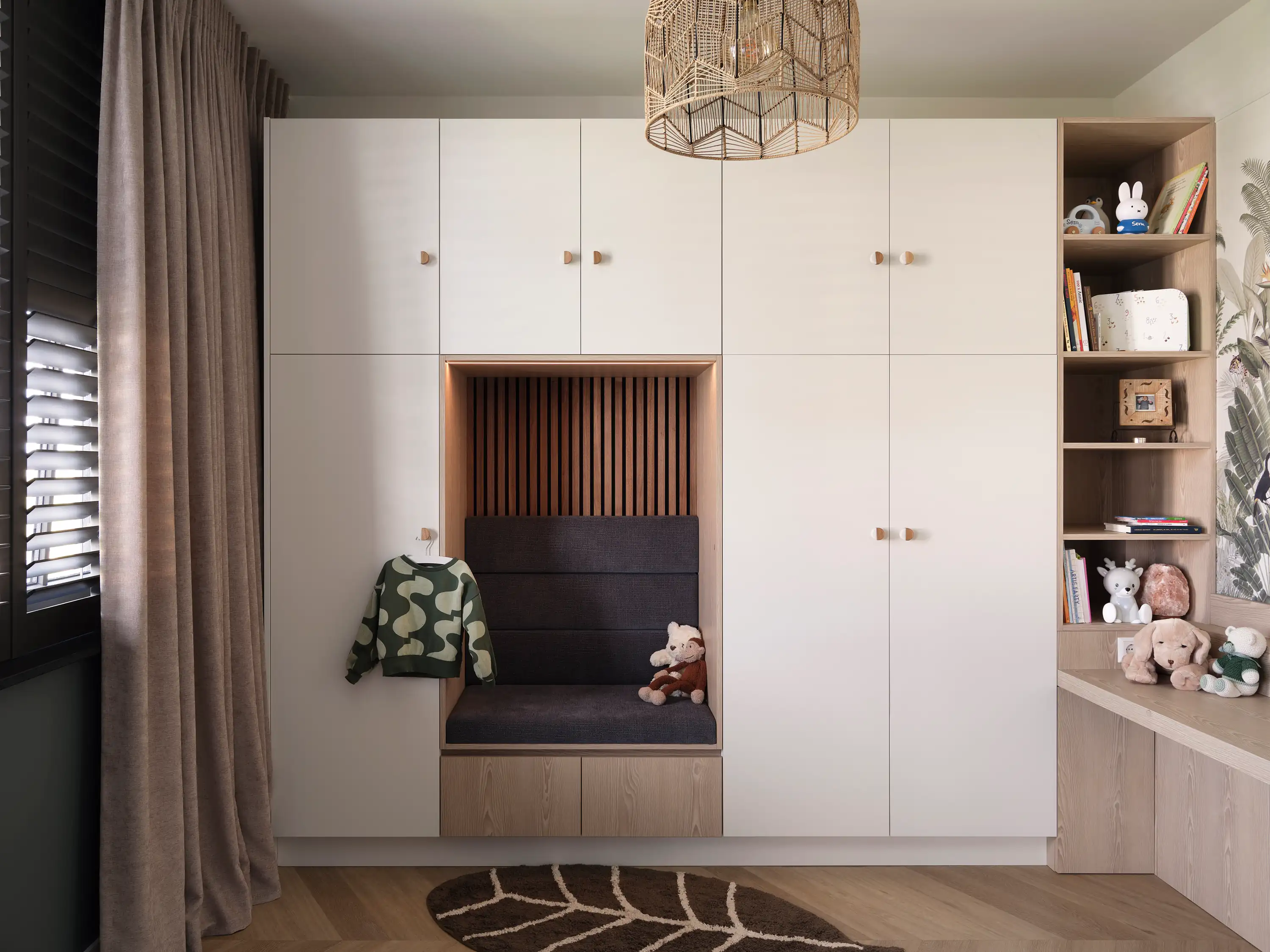
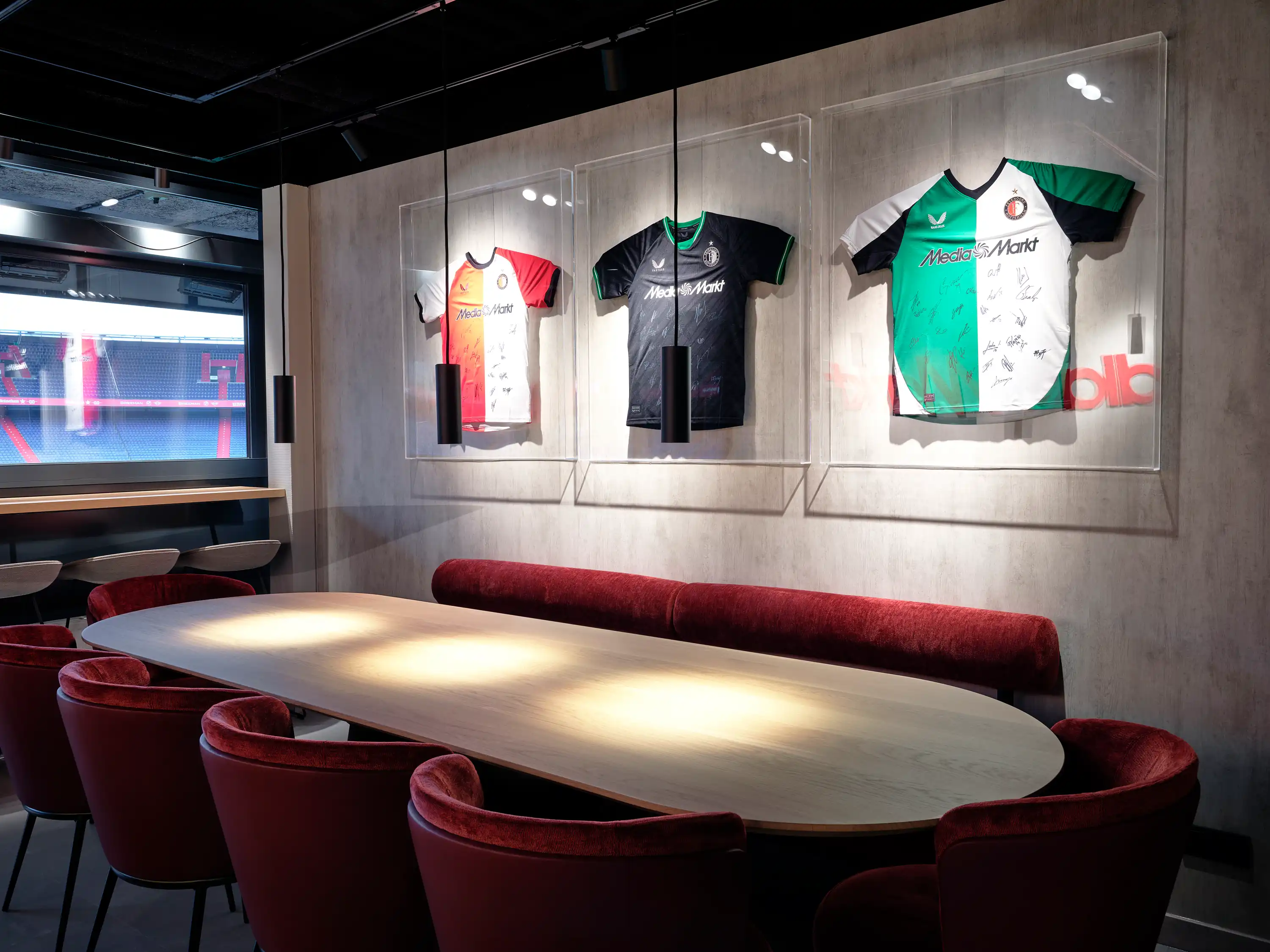
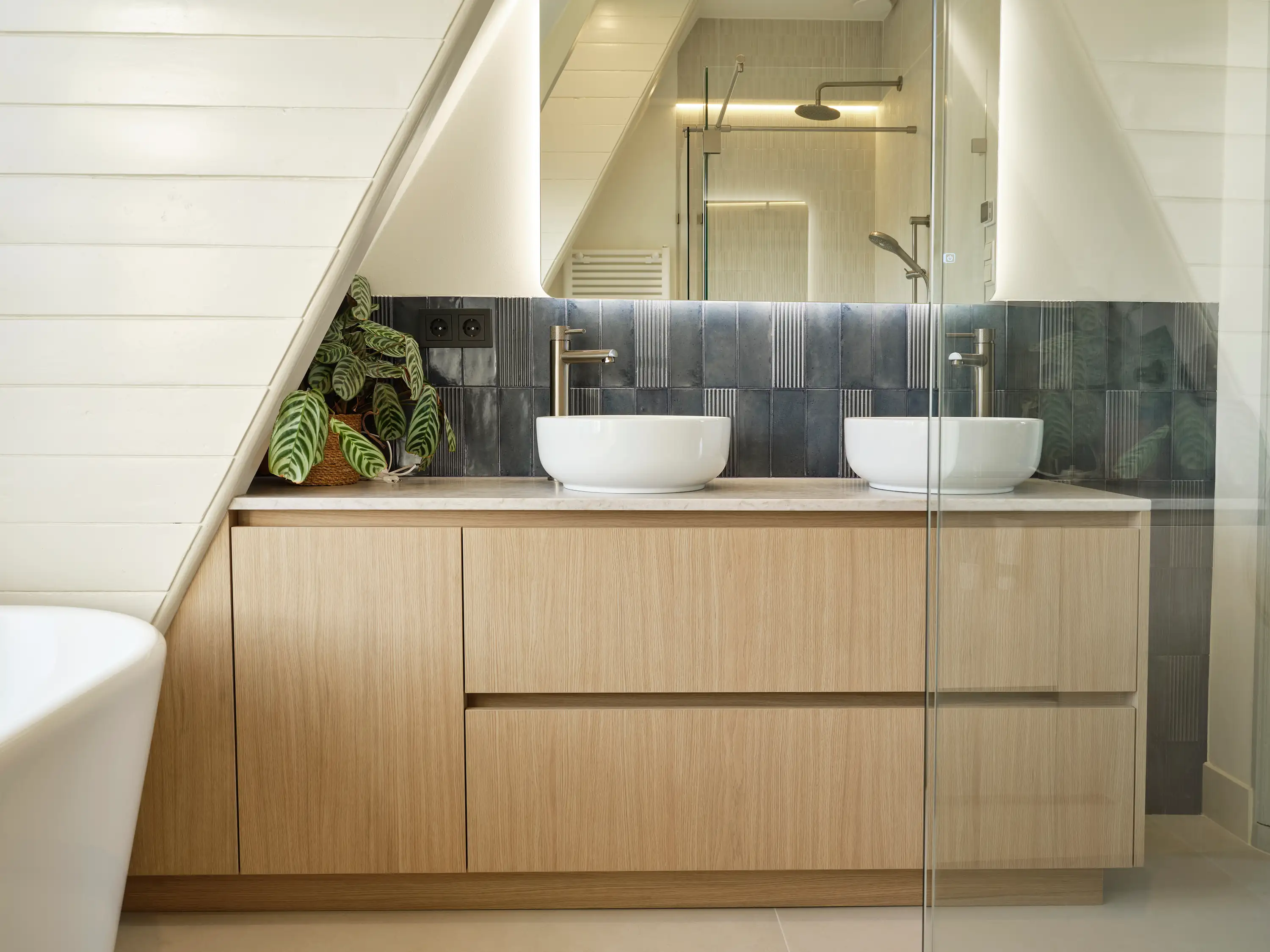
%20(1).webp)
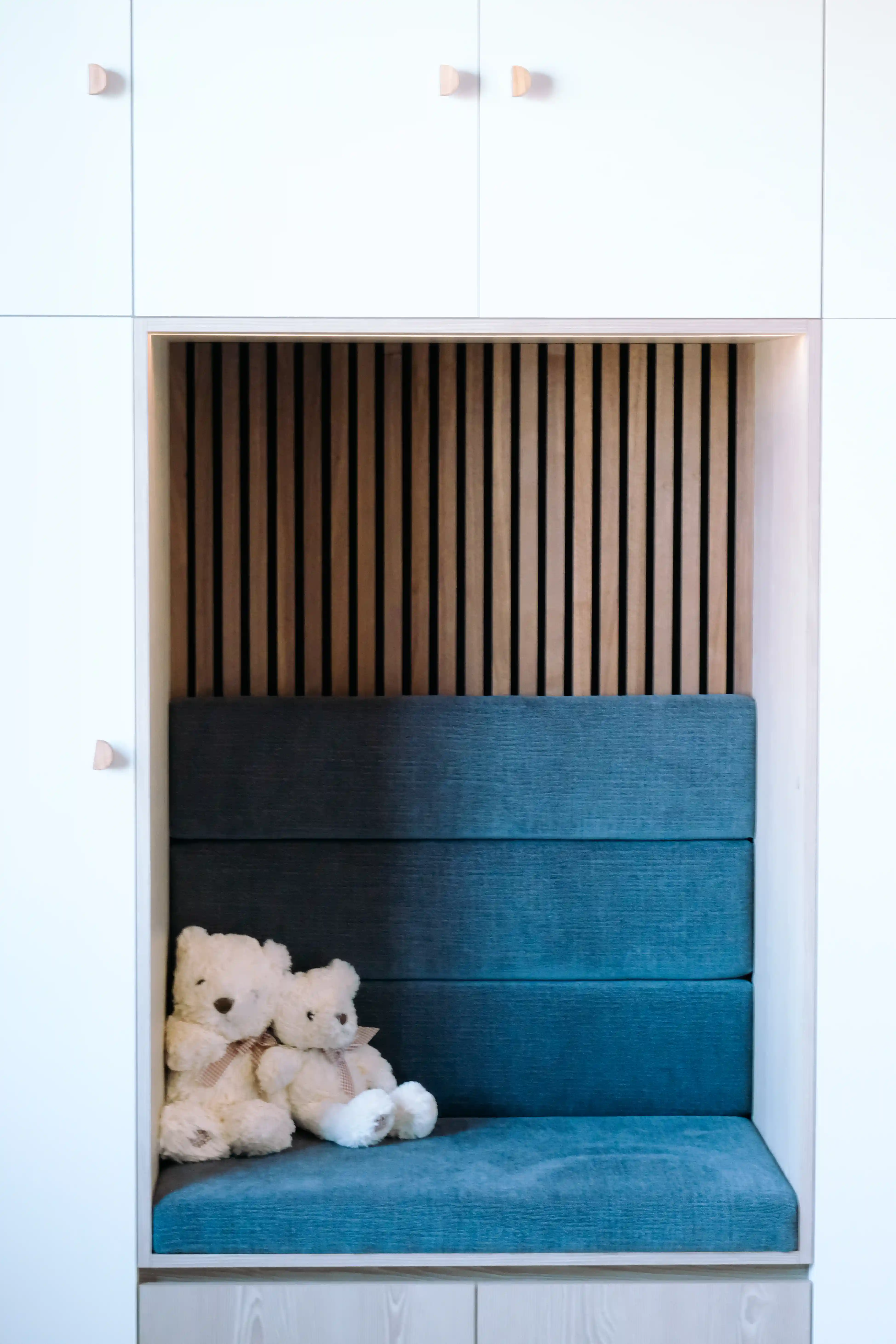
.webp)
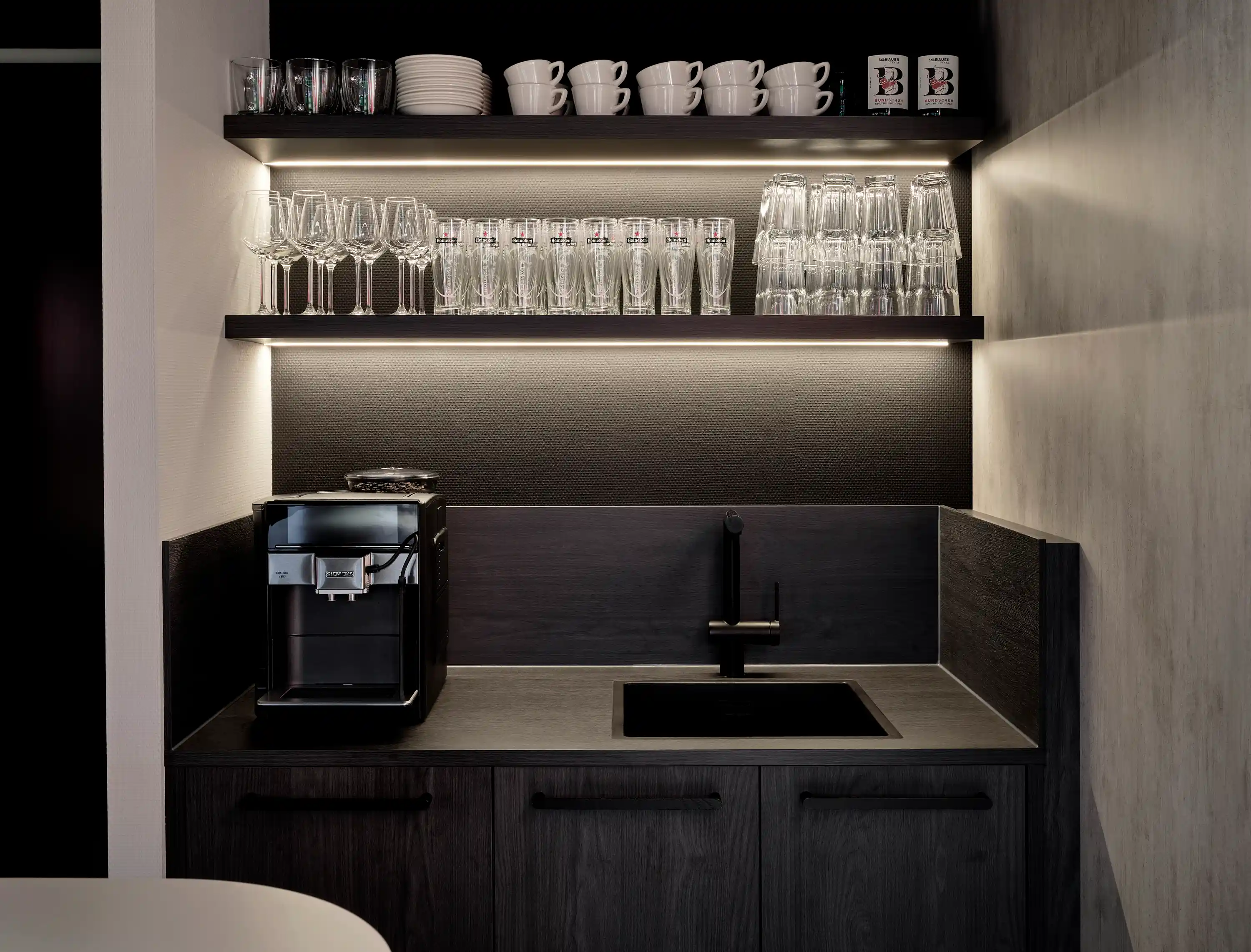
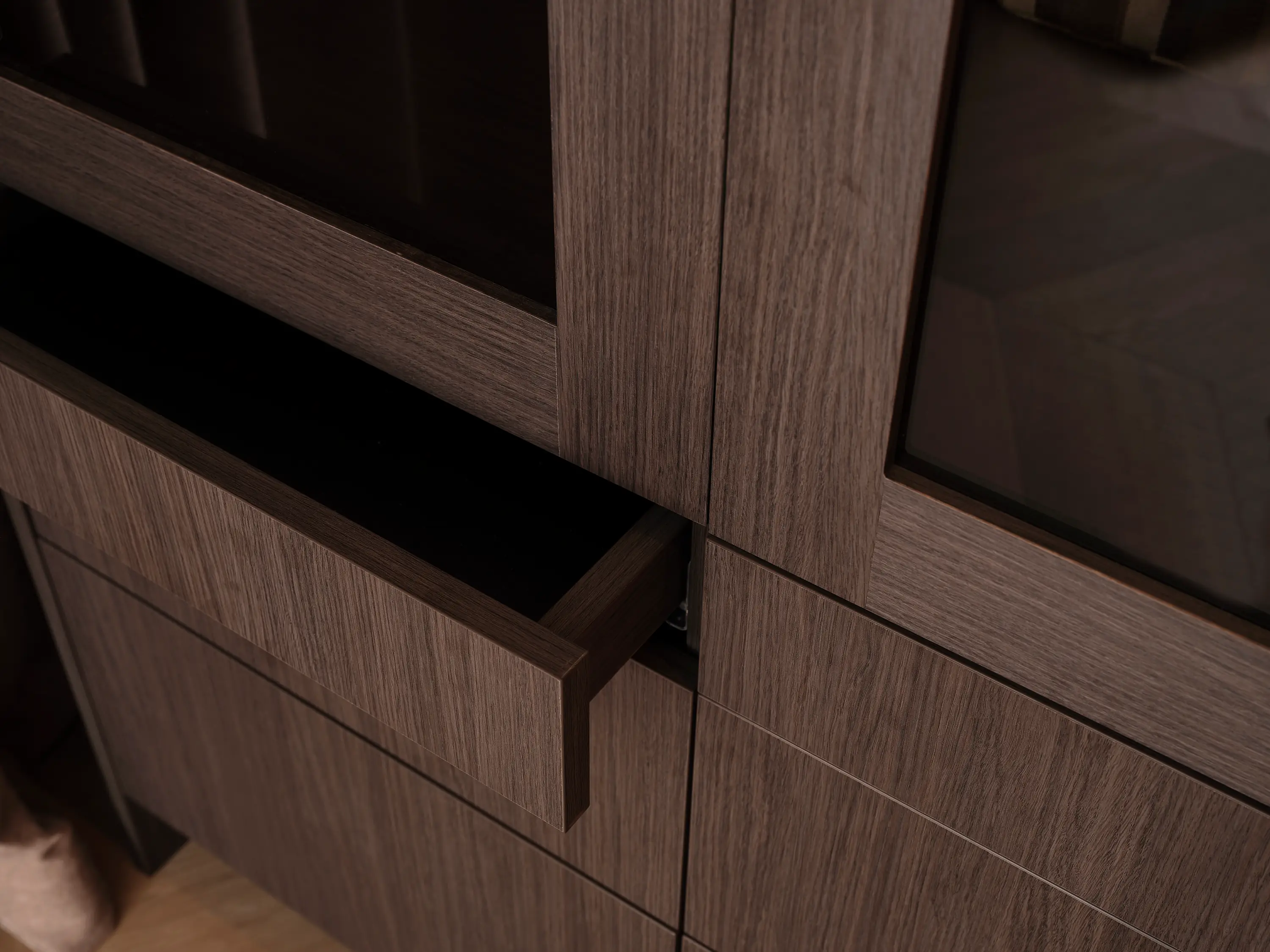
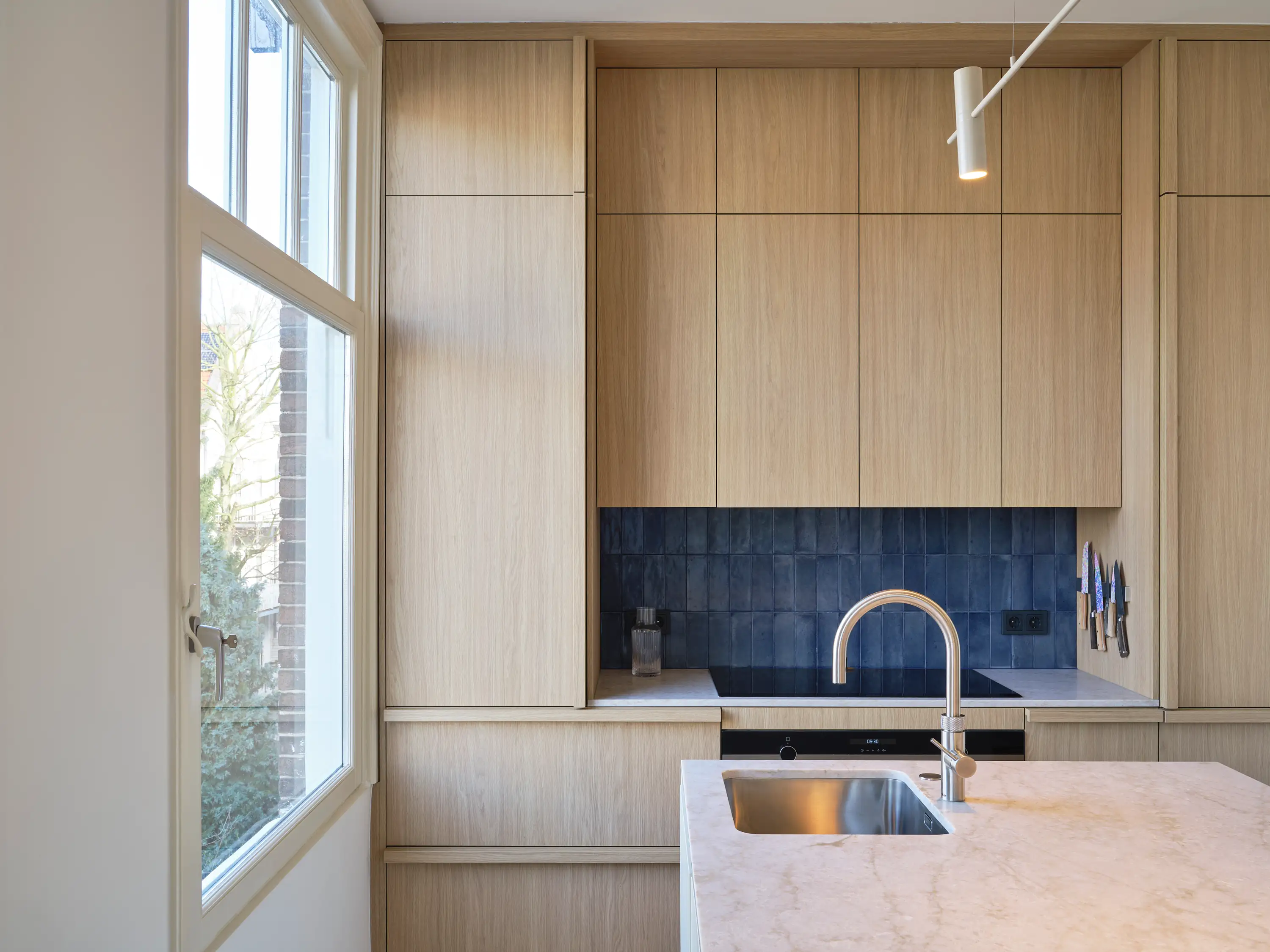
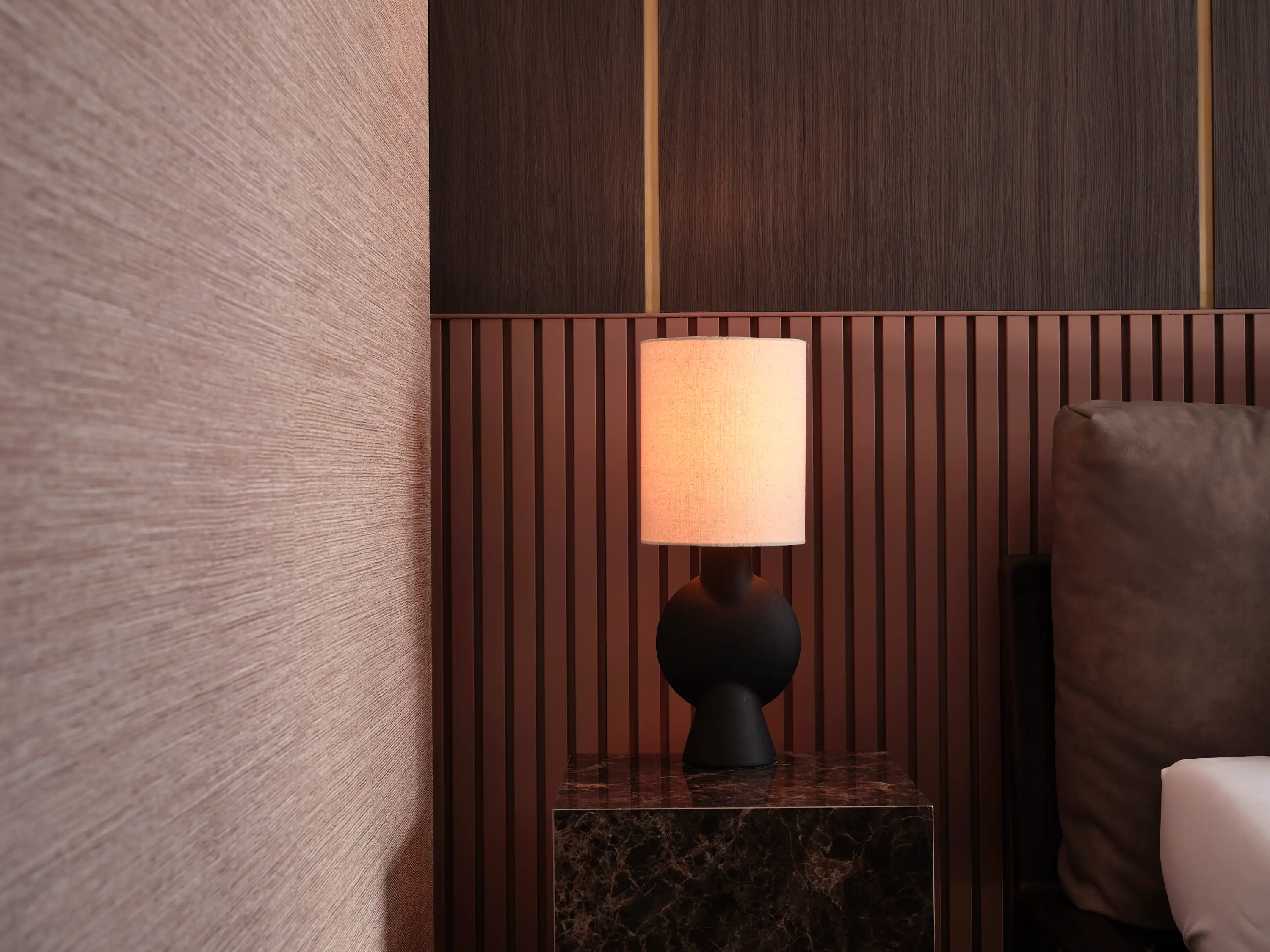
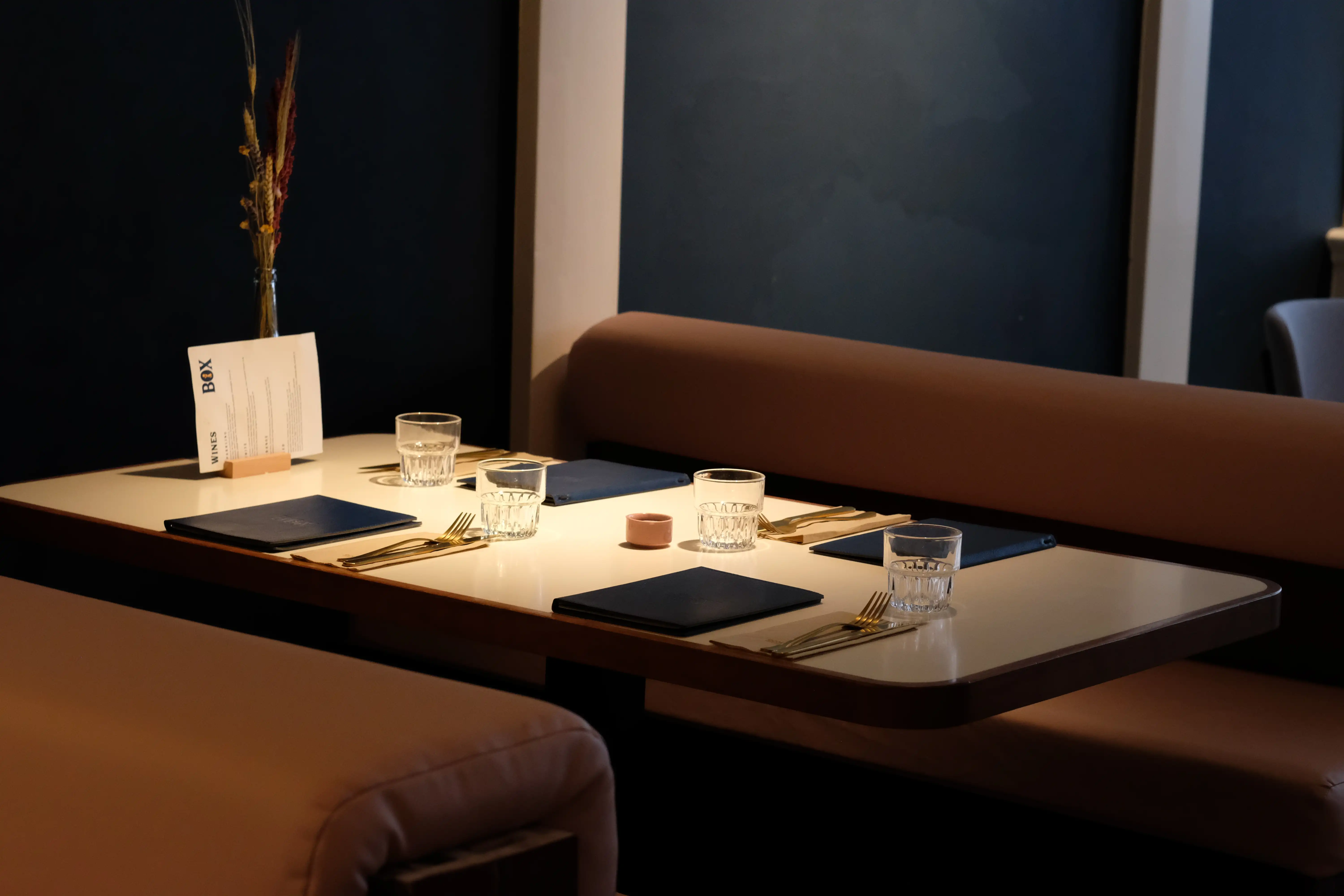
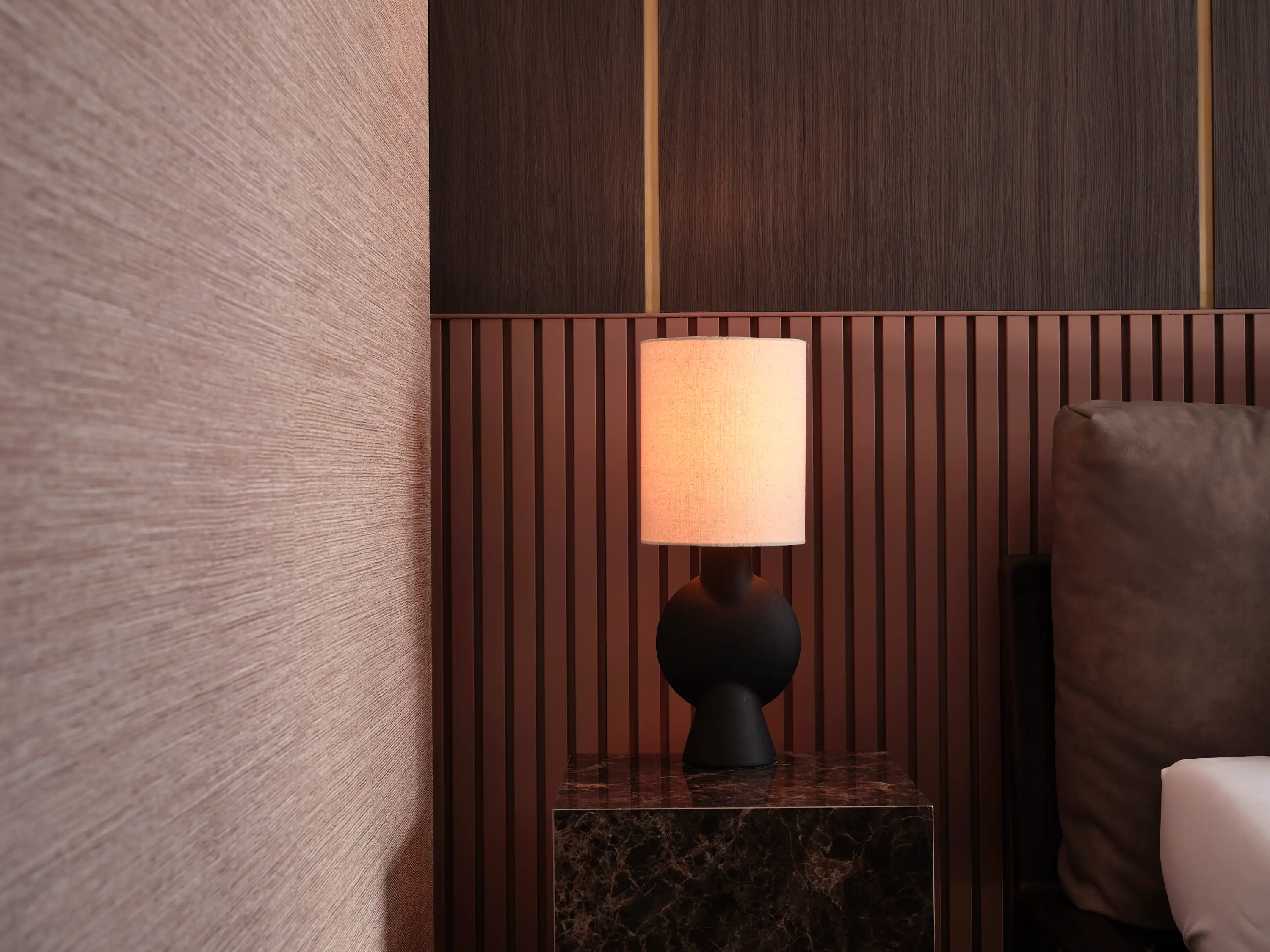