6 Steps to Produce High Quality Yacht Interior for Builders
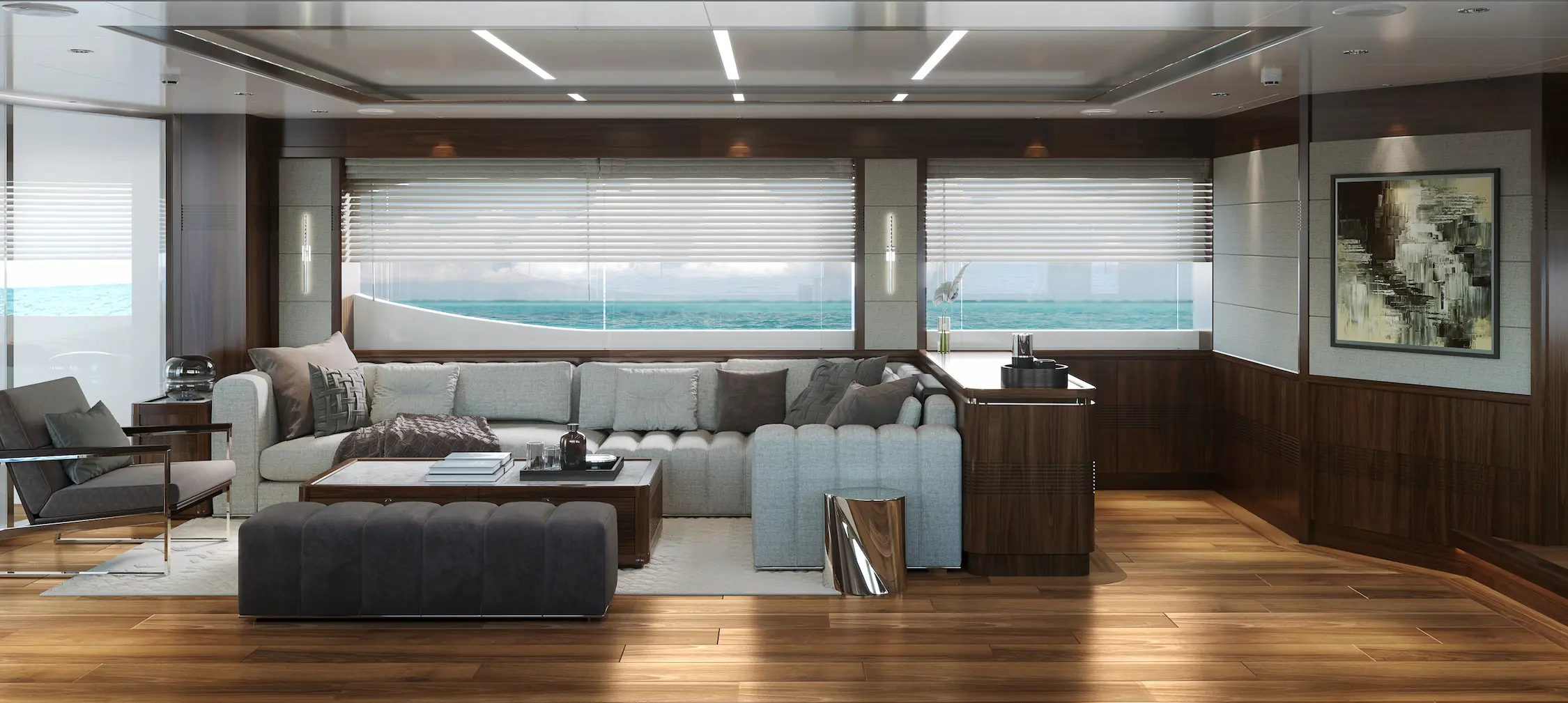
Interior construction for yachts doesn’t always run like clockwork
Building custom wooden interiors for yachts is a challenge in several areas. Think of things like:
- Dimensional stability and measuring
- Having the right drawings and cross-sections
- Supplementing 2D drawings with 3D drawings
Also, tolerances are an important consideration when building yachts. Just like the accurate measurement of double curved surfaces and tapered surfaces. In addition, frames and the ribs of the yacht must be precisely sized at every X centimetre, and fitting battens, finishing battens and cornices must also be perfectly tailored.
Not to mention unique challenges in yacht building with regard to its (watery) conditions.
Unique circumstances regarding ships at sea
After all, what happens to solid wood in wet places? And in what way do large differences in temperature, influenced by moisture and the sun, influence wood’s expansion and contraction?
First of all, a focus on good paintwork and varnishing is essential. Varnishing is very intensive and often requires two-component varnish. This must be done on location and it’s important to ensure the varnish is applied layer upon layer. A high-gloss finish is often required, which means that 4-8 layers of varnish and lacquer must be applied.
On top of that, sanding needs to be done in between those layers, with a grit that’s increasingly less coarse. During the varnishing process, you’ll need to vacuum away any excess dust by creating overpressure.
While you’re busy with all of the above, it’s not always possible to work on the yacht itself. With all the financial consequences this entails.
Additionally, every single thing should fit 100% perfectly. You can’t just sand away minor mistakes or fill some holes afterwards.
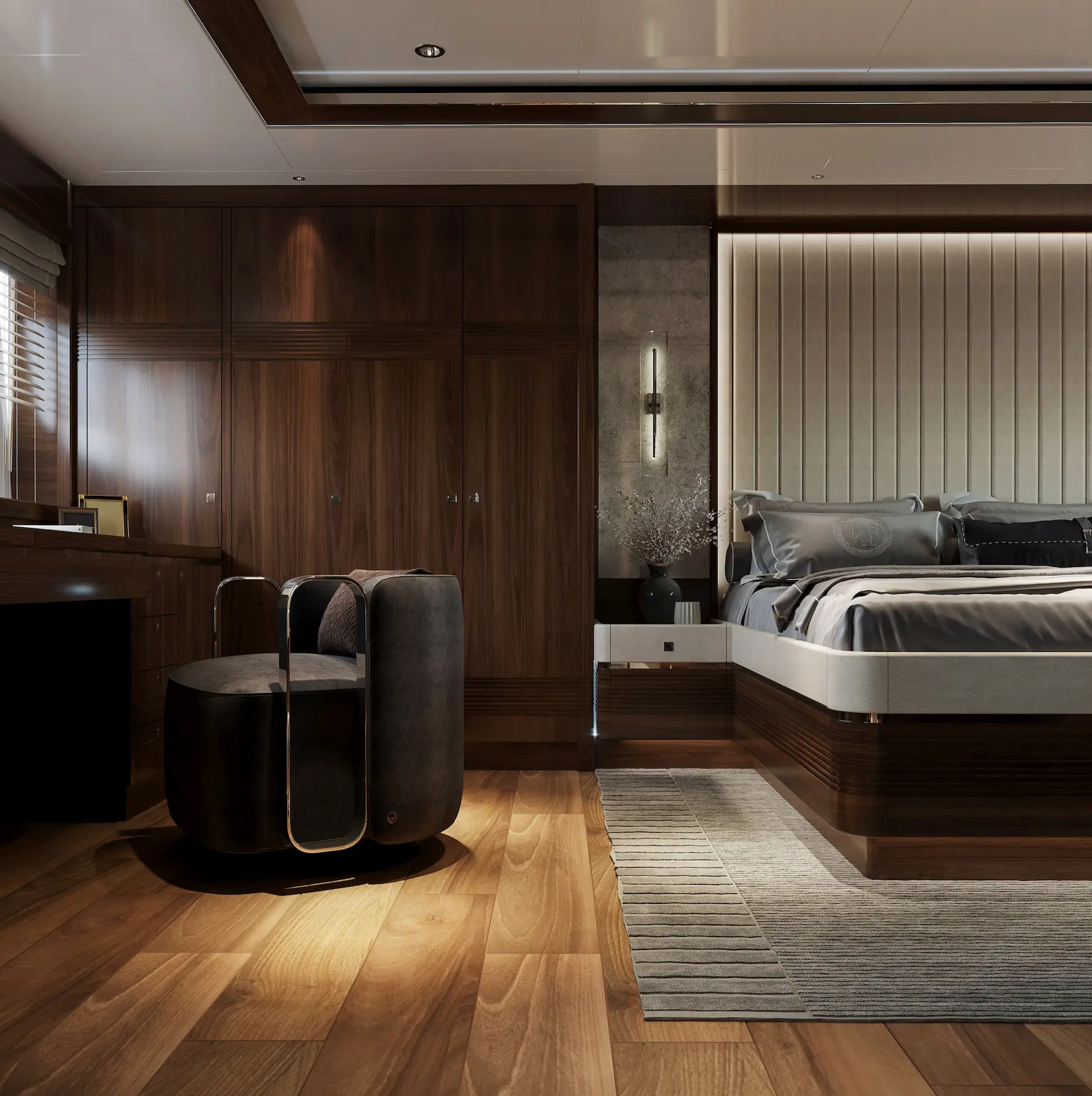
Make sure you remain in control of delivery times
When it comes to building yachts, customers are king, and often quite demanding at that. Be aware of the following challenges:
- Last minute amendments
- Revisions in drawings
- Designs that need to be adjusted in between
- Running overtime
You have to ensure you never work with old or outdated design files, so chances of making mistakes in production are minimised.
Naturally, you’ll also want to receive all materials in time, and focus on quality over quantity, all while remaining flexible with customers. Tight control over material delivery time is of the essence, here.
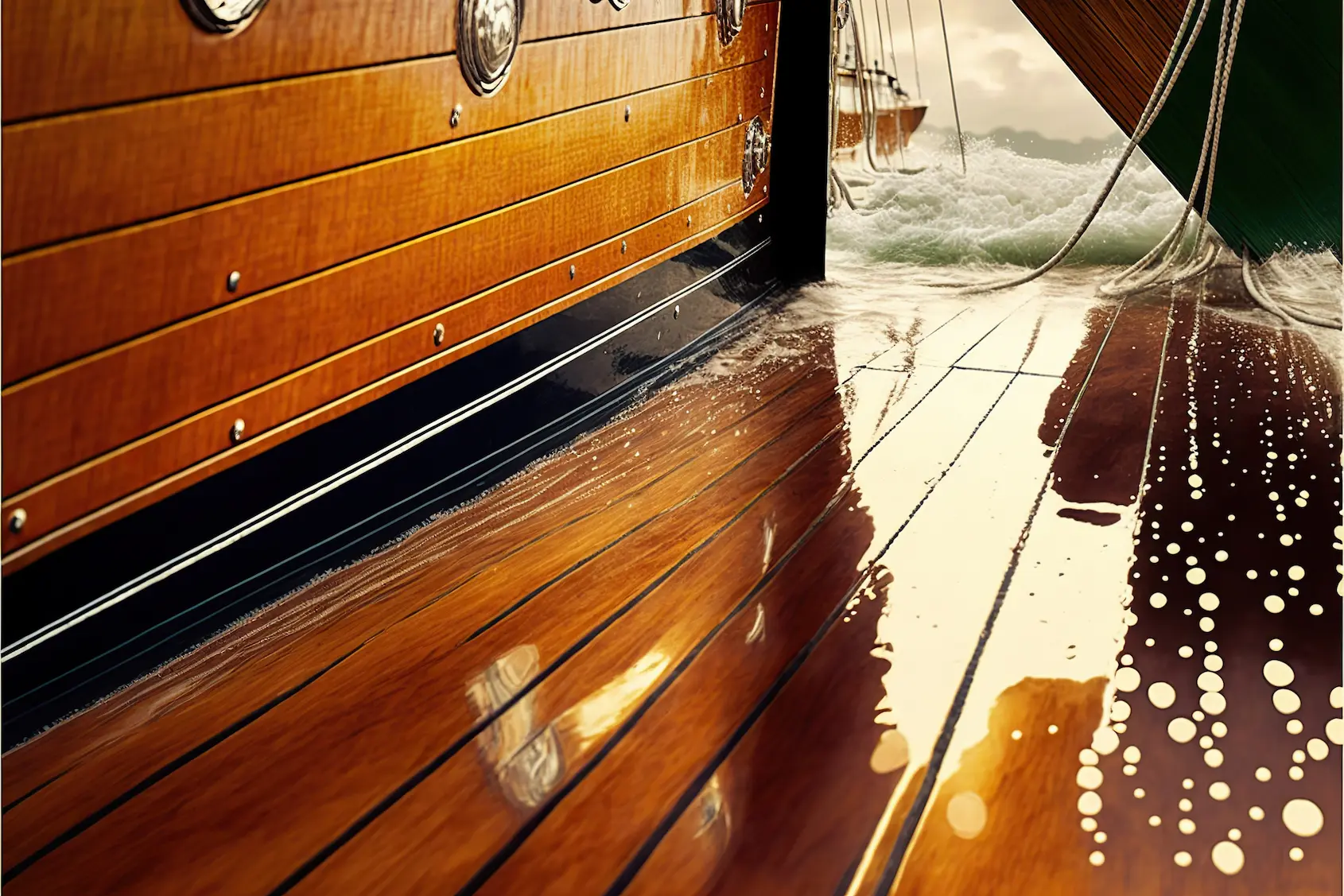
Improve the production quality of your yacht interiors
When building yachts, production quality is of the utmost importance. Not only when it comes to the technical aspects of construction, but also when working on detailing and the surface finish.
It’s equally important to clearly determine what can and cannot be implemented, and to take this into account during production. A team with high quality standards is essential for delivering a high-quality end product. However, there’s still a risk of human error. Which is why you should carry out good quality control and work with checklists.
Proper communication and trust among team members helps prevent miscommunication when making revisions and adjustments. Focus on improving this, and the work can be done more quickly and efficiently, ultimately refining the end result’s production quality.
Finding the perfect prefab production partner is crucial
To improve the delivery time and quality of prefab interior projects in yacht building, you need the right production partner. Such a production partner is able to:
- Run partial productions
- Deliver semi-manufactured products
- Create more building kits
- Take measurements in advance
A good production partner can also work with tailor-made fitting laths or end panels. The rest is done in a standardised way in the workshop. You should take into account the following distribution: 90% standard work, 10% made to fit on location.
By building mockups in modules and hoisting them on board later, kind of like you would a LEGO set, the entire process is significantly sped up.
Experts should supervise the production process of these complex projects
To guarantee the highest possible quality in interior construction for yachts, it’s best to work with real experts. If the entire production process is closely monitored by experts, there’s little risk of anything going wrong.
Like we said before, expectations in yacht building are extremely high. Guidance from experts can help manage these expectations.
These experts can take responsibility as points of contact, share their extensive knowledge and offer high-level consultancy, while you build trust with your customers. Your customer will both sense and be set at ease by this expertise, as well as see it reflected in the quality of the end product.
Conclusion
To ensure the best possible quality in yacht interior construction, it's best to work with experienced professionals. Closely monitoring the entire production process reduces the risk of anything going wrong.
Related articles:
The top 3 reasons for delays to your projects and how to solve them
Upload your design file and get a quote
within days
Quality production with trusted production network.
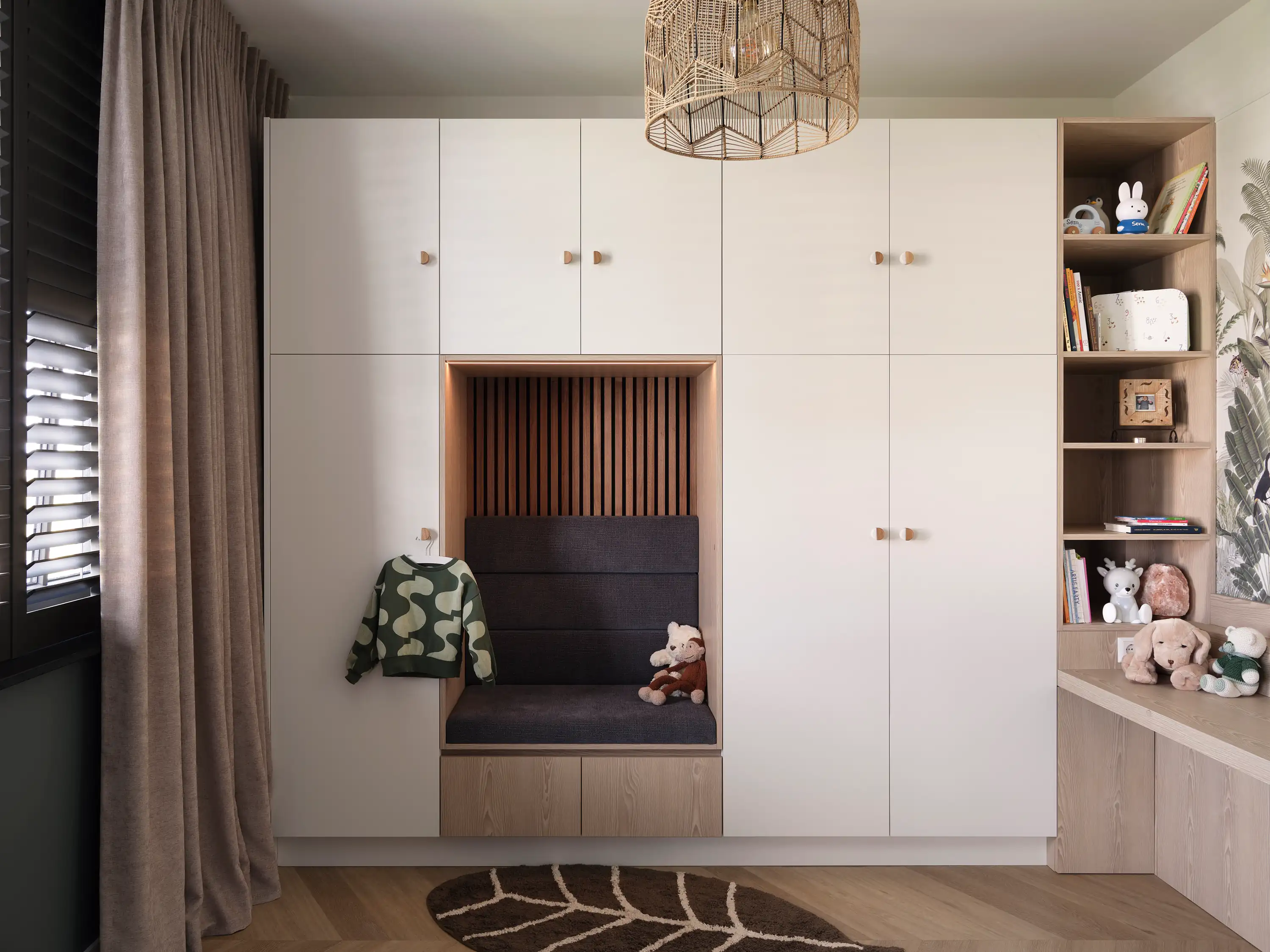
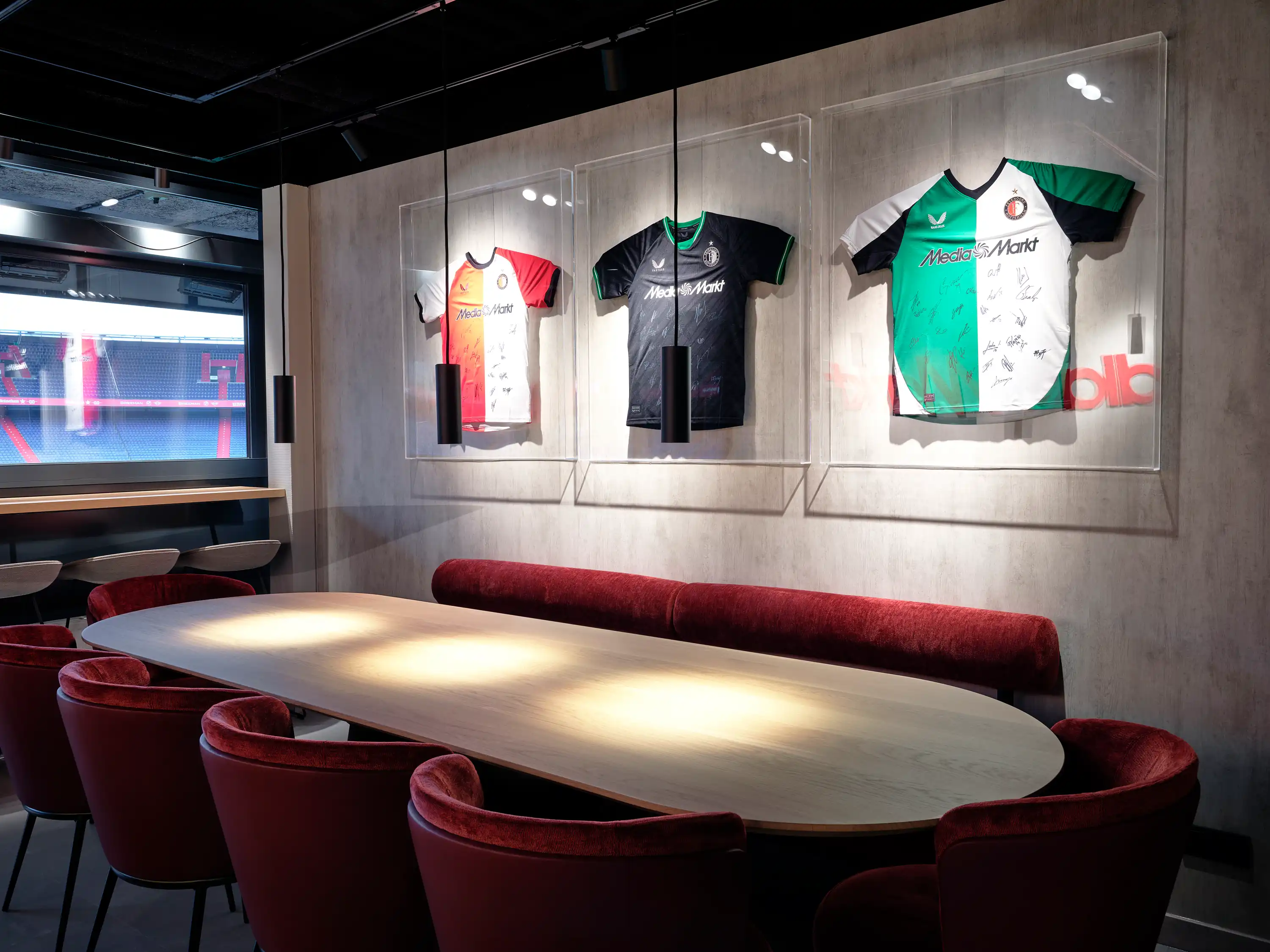
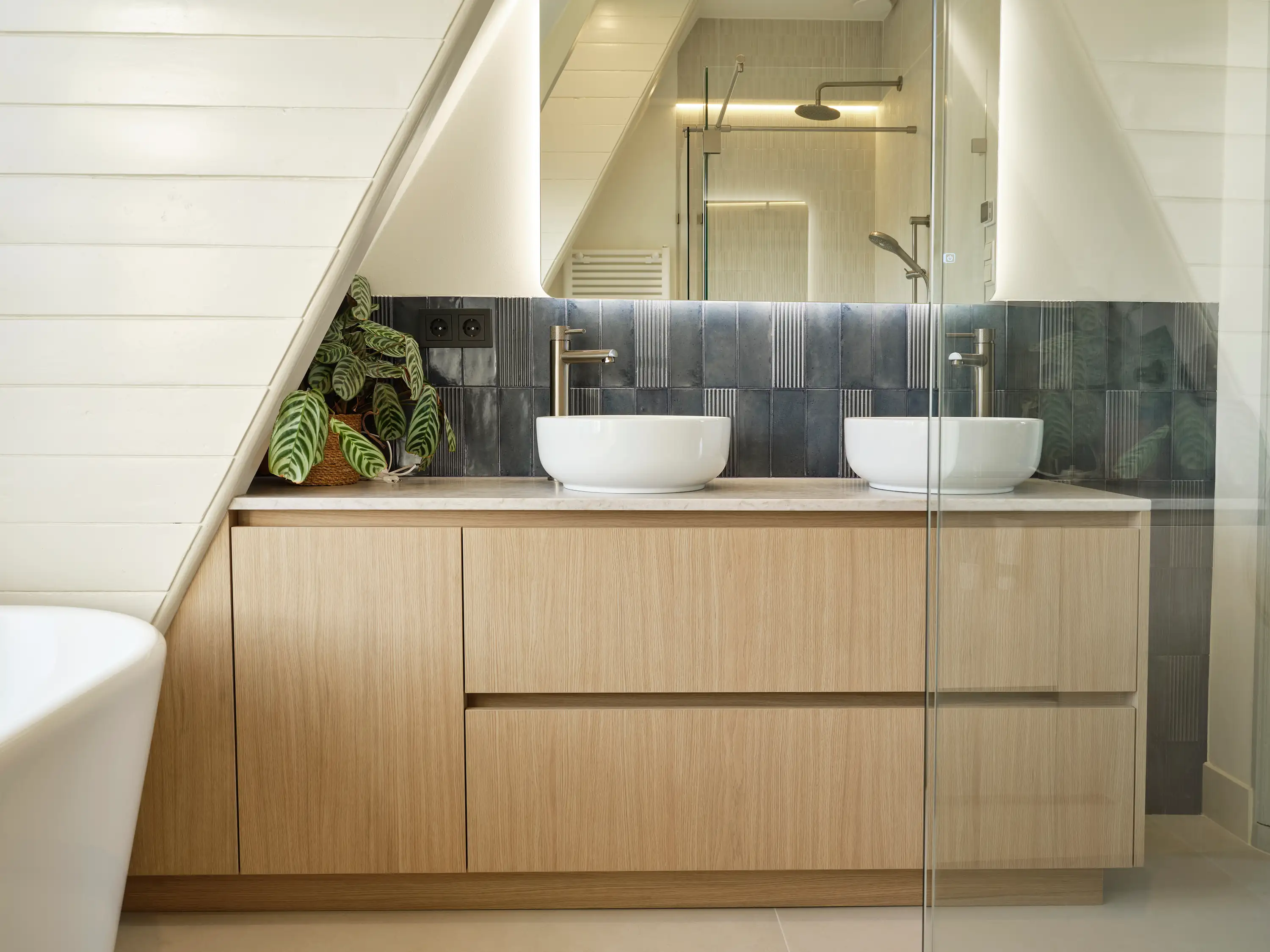
%20(1).webp)
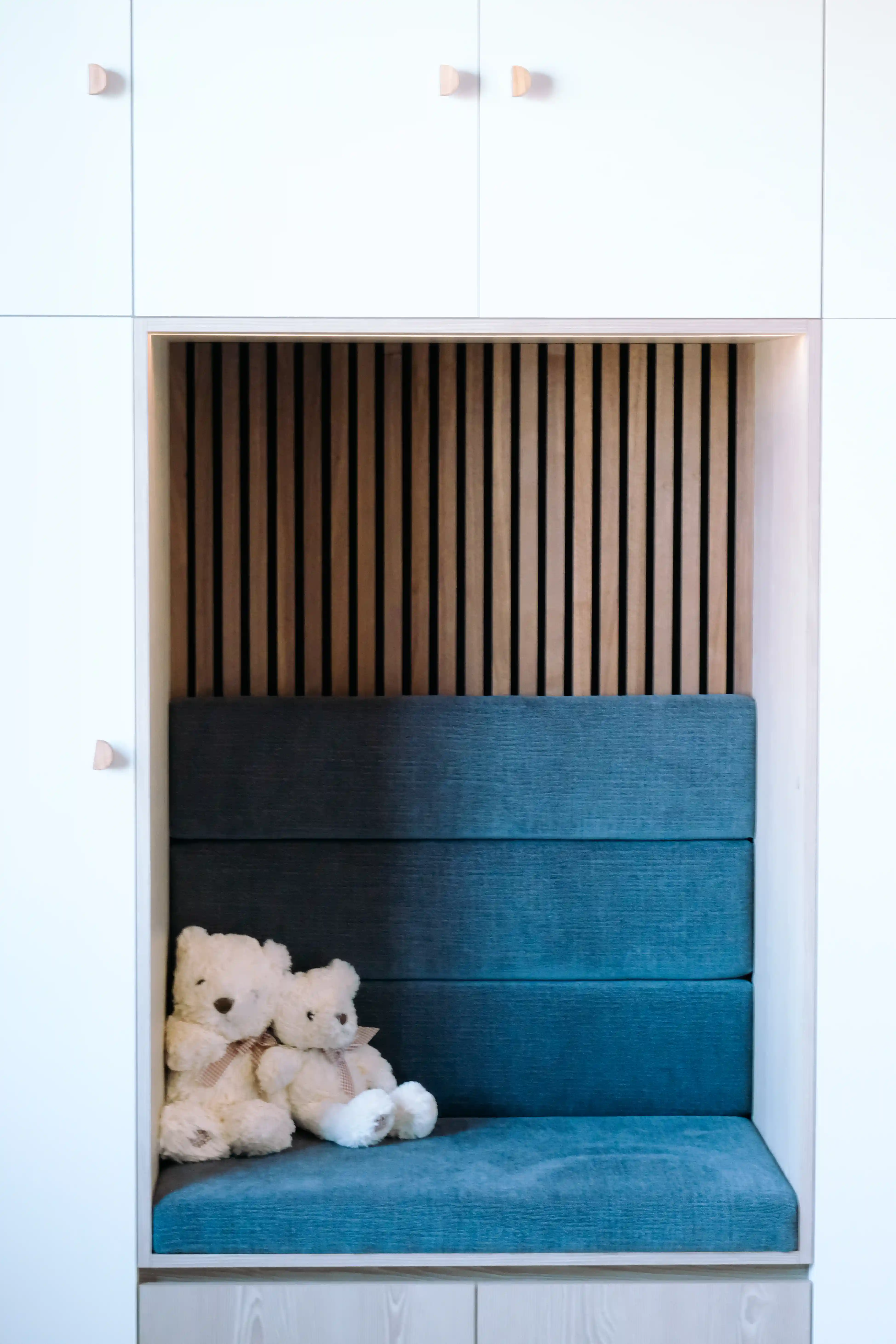
.webp)
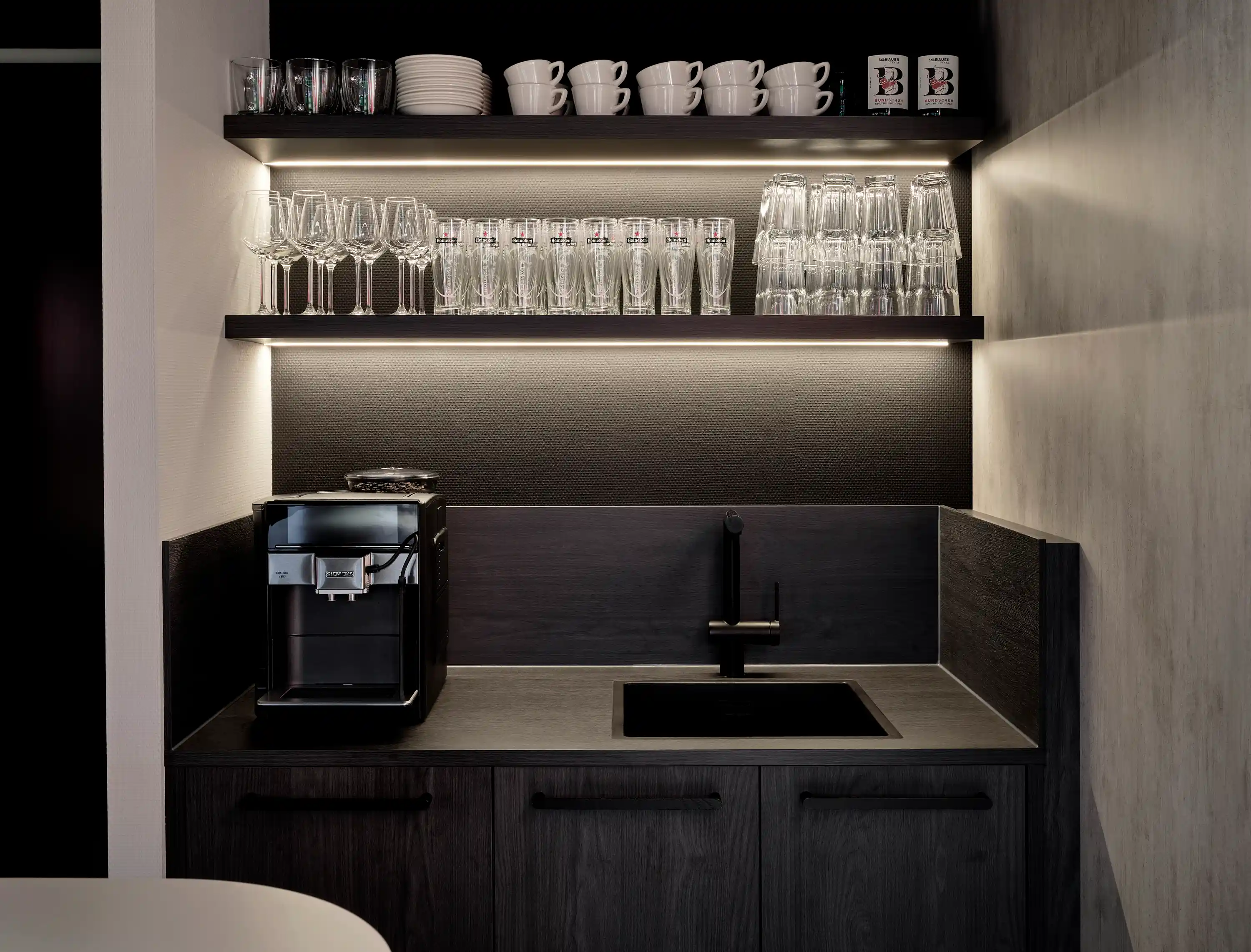
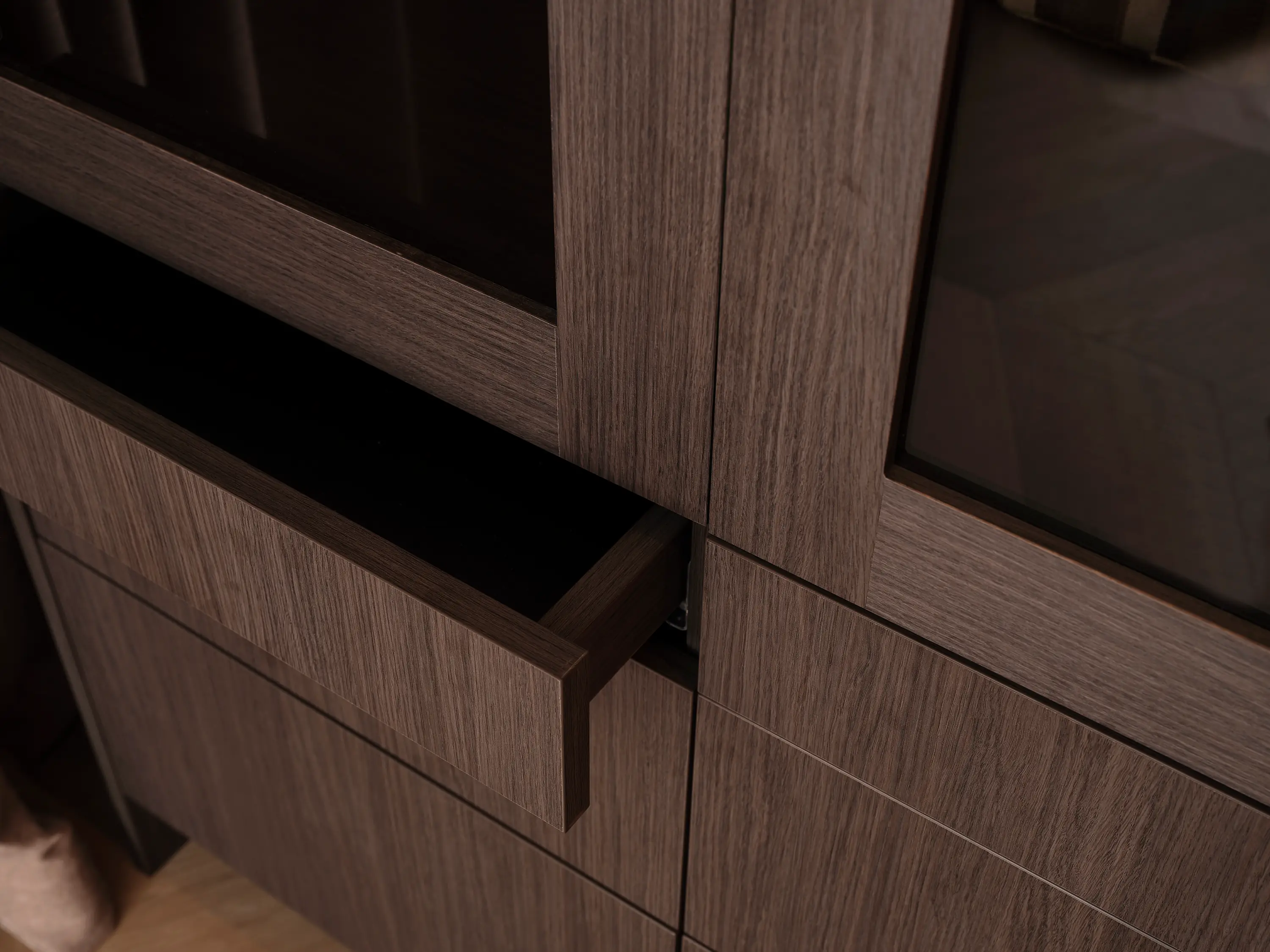
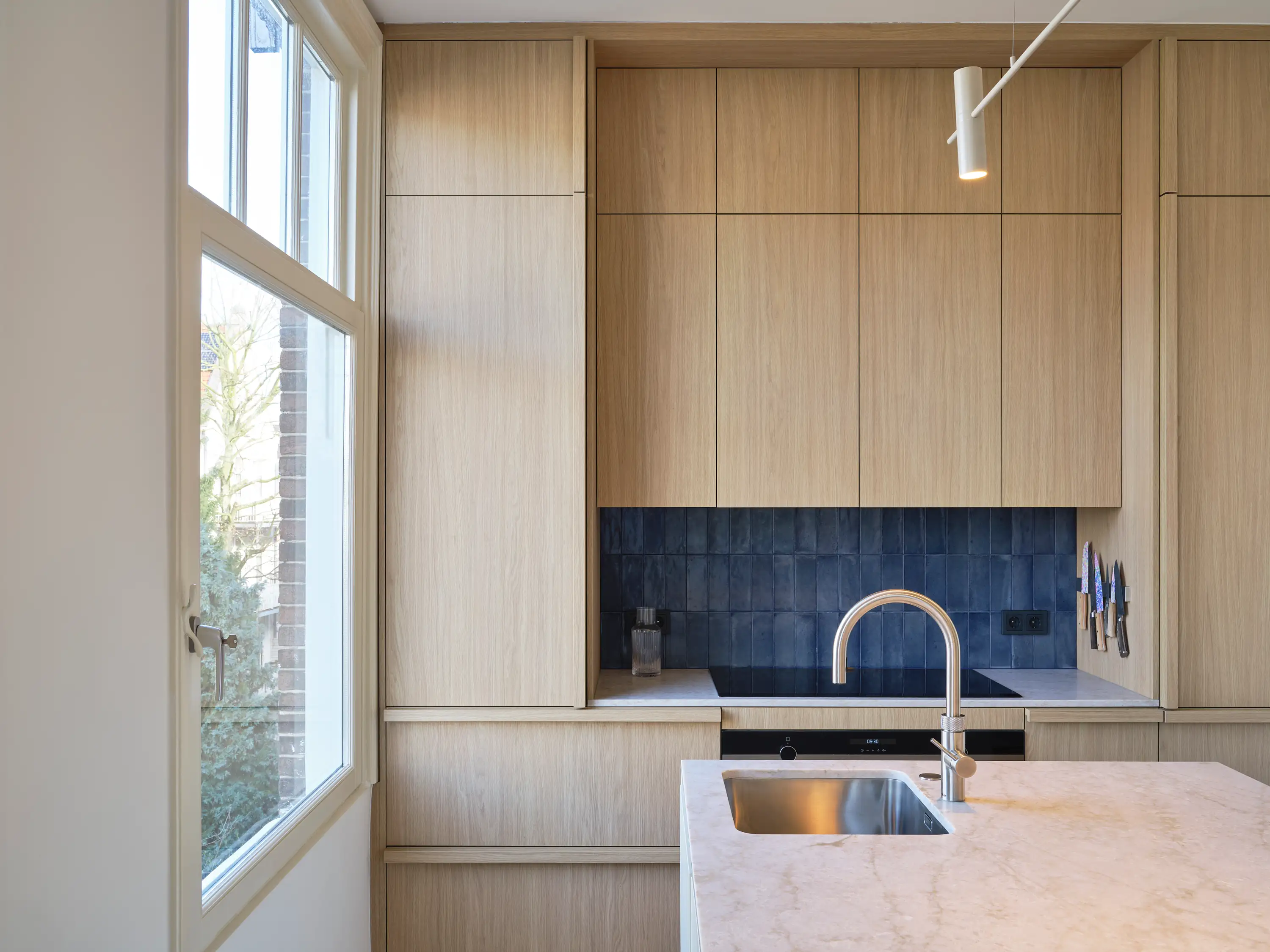
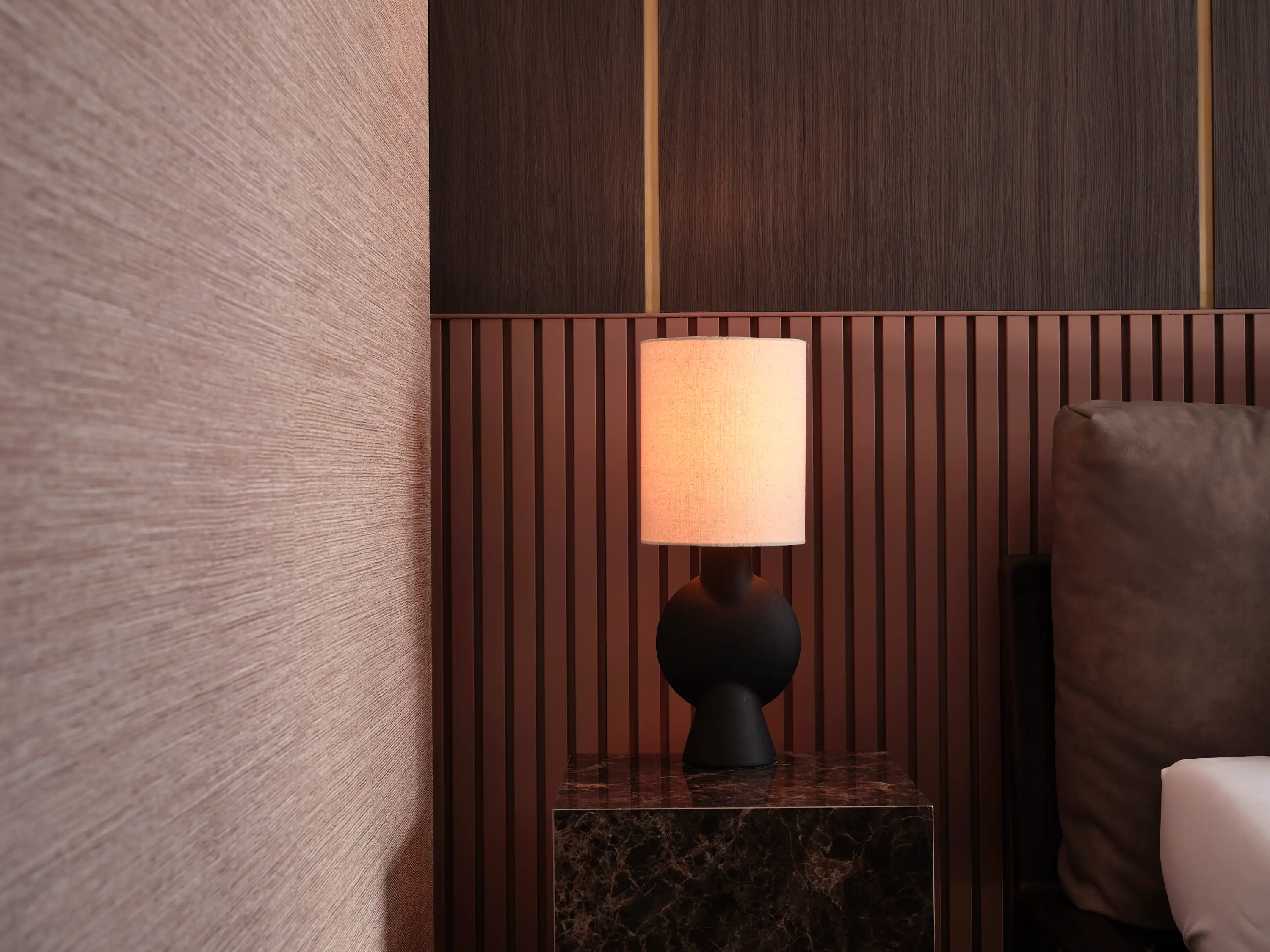
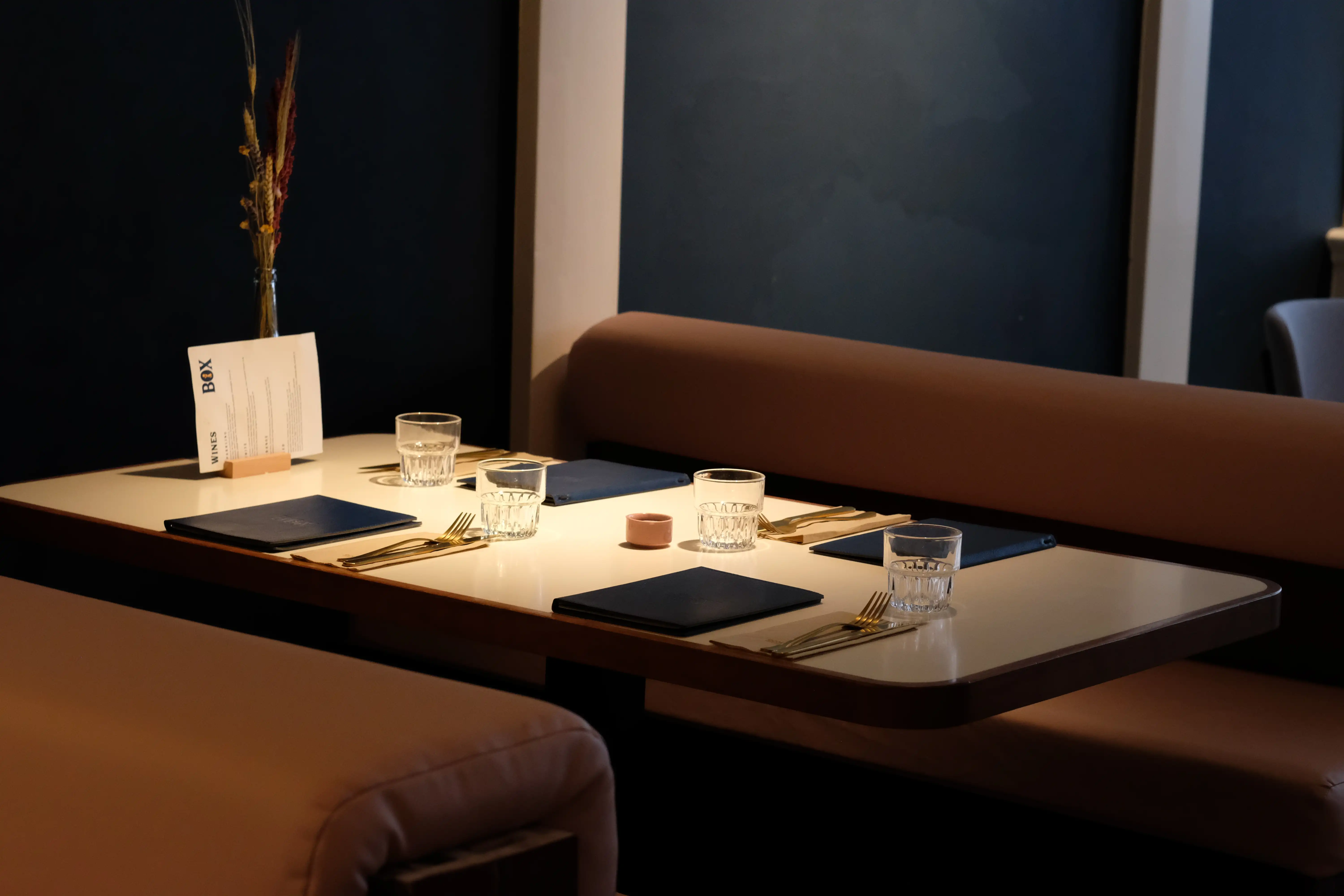
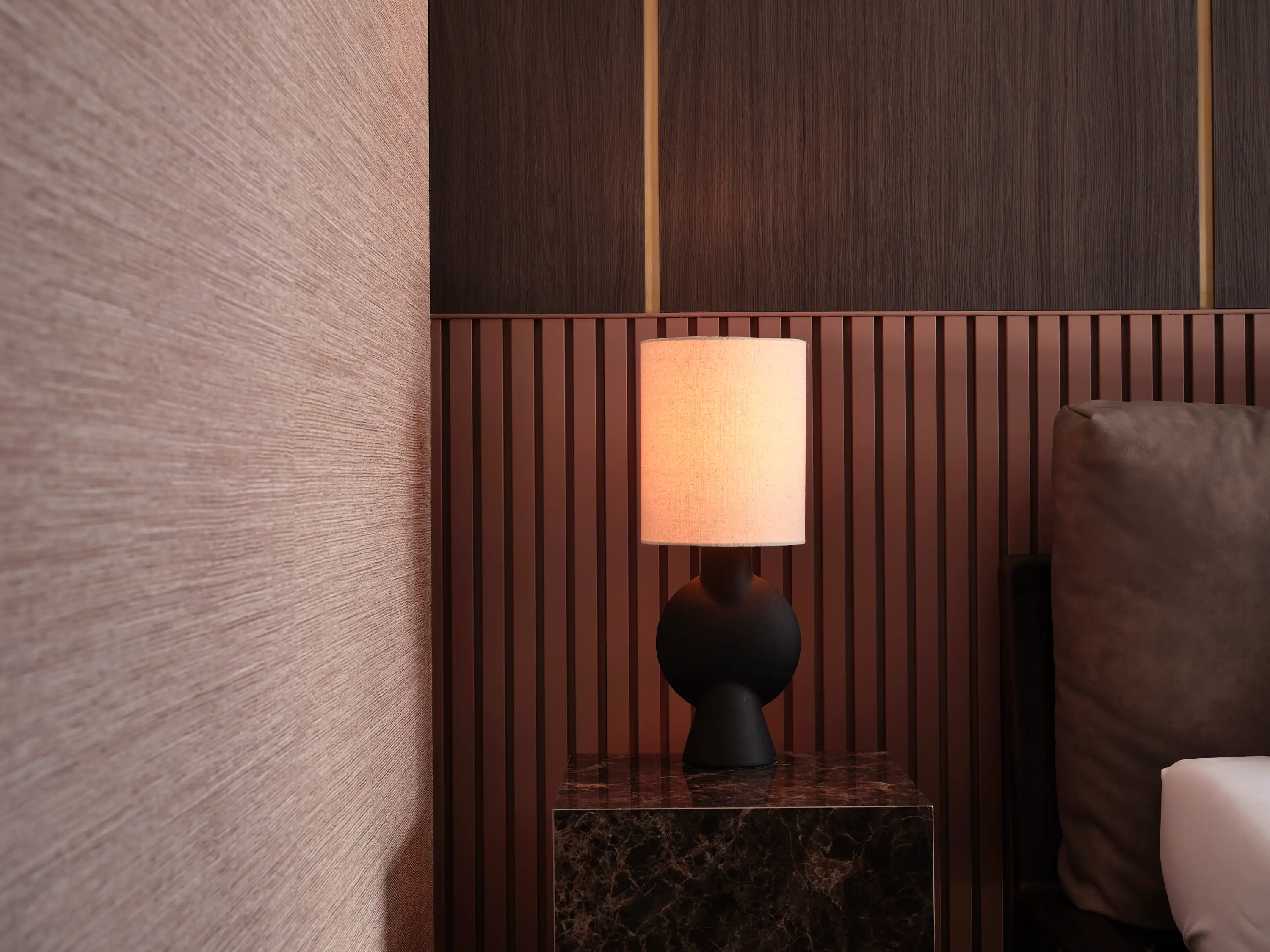